Em usinas de geração de energia em todo o mundo, milhões de motores críticos de baixa tensão operam sem monitoramento. Isso pode reduzir sua eficiência e resultar em paralisações não planejadas e de alto custo, além de interromper a produção de energia. Entretanto, isso pode ser evitado quando medidas de manutenção preditiva são adotadas para monitorar os motores nas usinas.
Manutenção preditiva para garantir a produção de energia
De acordo com o artigo da BehrTech, cerca de 70% das indústrias não sabem quando os motores/ativos precisam de manutenção ou substituição. Isso gera muito material de manutenção parado em estoque e pode ocasionar paradas não planejadas na planta. Além disso, uma parada não planejada pode custar entre US$ 30.000 e US$ 50.000/hora no ambiente industrial.
No mesmo estudo, foi identificado que ambientes industriais com iniciativas de manutenção preditiva reduzem de 5 a 10% os custos gerais de manutenção. Por isso, a Macnica DHW trouxe com exclusividade para o Brasil a solução ADI OtoSense. Com ela, é possível reduzir em até 80% o tempo de inatividade não planejado dos motores da planta industrial.
“O dispositivo SMS da ADI OtoSense nos permite monitorar com eficiência os motores de máquinas importantes em nosso processo de geração de energia. Entre eles, estão ventiladores de refrigeração de turbinas a gás, bombas de controle de óleo hidráulico ou bombas de refrigeração de circuito fechado. Assim, otimizamos a medição das vibrações manuais, economizamos horas-homem de manutenção e evitamos o acesso de operadores a locais perigosos ou elevações.”
Gonzalo Gracia De La Rosa, Gerente de Planta de Manutenção Naturg.
Veja, a seguir, como essa solução inteligente para manutenção preditiva já está trazendo resultados positivos no mercado de geração de energia.
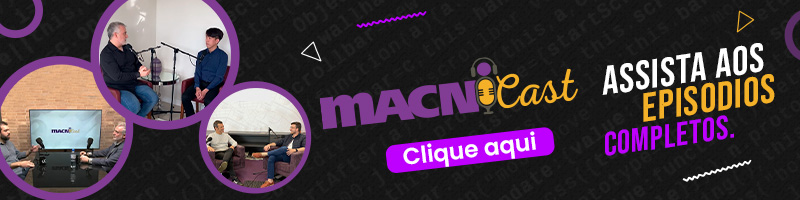
Solução ADI OtoSense aplicada em uma usina de geração de energia
Uma das principais dificuldades ao monitorar motores e ativos em usinas de geração de energia é que eles, geralmente, estão em áreas enormes. Para completar, esses espaços costumam ter condições ambientais extremas e flutuações de temperatura.
Essas condições ambientais dificultam a medição de som e vibração dos motores e a identificação do seu nível de funcionalidade e possíveis falhas. Todos esses detalhes tornam impraticável o monitoramento contínuo tradicional.
O sensor inteligente ADI OtoSense fornece uma solução de manutenção preditiva sem precedentes para usinas de geração de energia. Veja algumas funções que ele realiza:
- resolve o problema de monitoramento contínuo da saúde de motores de indução críticos;
- fornece insights em tempo real para a rápida tomada de decisão dos responsáveis pelo local;
- gera maior economia de custos por meio de uma análise aprofundada da integridade do motor.
A solução ADI OtoSense não substitui os especialistas. Pelo contrário: ela aproveita sua experiência e seu conhecimento sobre motores para ajudar a solução SMS da OtoSense a reconhecer problemas no início. Com isso, a eficiência e a produtividade do motor aumentam, impactando positivamente os resultados de uma empresa. Veja, a seguir, como foi a sua aplicação em uma usina de geração de energia.
Objetivo
O principal objetivo do cliente era monitorar os motores de uma usina de geração de energia para aumentar a produtividade e a eficiência.
Desafios
O ambiente hostil de uma usina, assim como muitos ambientes industriais, apresenta diversos desafios para a implementação de sistemas de monitoramento, como:
- observação de som e vibração dos equipamentos, principais indicadores de desgastes e falhas, em locais grandes, quentes, barulhentos e nem sempre seguros;
- redução do tempo gasto pelos técnicos da equipe de manutenção, que precisam percorrer a fábrica, todos os dias, para detectar problemas nas máquinas;
- monitoramento constante de máquinas grandes e complexas com redundância limitada;
- redução de paradas na usina, causadas por falhas em equipamentos secundários, como bombas e ventiladores.
Solução e resultados
A partir da instalação da solução ADI OtoSense, foram implementadas as iniciativas de manutenção preditiva e proativa. Com isso, foi realizado o monitoramento contínuo dos ativos primários e secundários, como:
- bomba de água de resfriamento;
- soprador de fuligem;
- caixa de engrenagens;
- bomba de vácuo;
- estrutura de turbina a gás;
- ventiladores de resfriamento de rolamentos.
Com os dados coletados e analisados pela solução ADI OtoSense, foram alcançados os seguintes resultados:
- credibilidade operacional aprimorada;
- otimização da aplicação de recursos de manutenção;
- diminuição da manutenção não planejada;
- redução do tempo de inatividade que gera altos custos;
- diminuição do número de operadores no campo.
Além disso, o sensor inteligente ADI OtoSense também pode gerar outros resultados positivos para a usina de geração de energia, como:
- redução dos custos de manutenção;
- redução de paradas imprevistas e falhas catastróficas;
- ampliação do período entre as revisões;
- redução das atividades baseadas em rota e otimização da aplicação de recursos de manutenção;
- gerenciamento de peças de reposição e estoque com mais eficiência;
- aumento da vida útil dos equipamentos;
- otimização da eficiência do motor;
- melhora na OEE (Eficiência Geral do Equipamento).
A imagem abaixo ilustra onde os sensores inteligentes ADI OtoSense foram instalados na usina de geração de energia. Para saber como ter esses resultados na sua indústria, clique aqui e entre em contato com a gente.
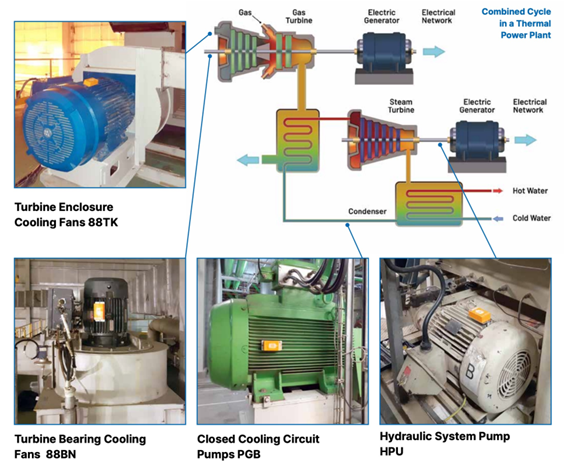
Sensor inteligente ADI OtoSense instalado em áreas importantes das usinas de geração de energia.
Fonte: ADI OtoSense
Mais benefícios da solução ADI OtoSense
Como você viu, a aplicação da solução ADI OtoSense trouxe diversos resultados positivos para a usina de geração de energia. Mas não para por aí: veja, abaixo, mais alguns benefícios que essa solução pode proporcionar para a sua empresa.
1 – Diagnóstico avançado para itens de ação priorizados
- Falhas elétricas e mecânicas são diagnosticadas em seu início.
- O nível de severidade ajuda a priorizar a manutenção necessária.
- Recomendação sobre ações necessárias.
2 – Tecnologias de detecção para análise de dados de alta qualidade
- Sensores de vibração de largura de banda ampla e multieixo.
- Sensores de campo magnético para monitorar a saúde elétrica do motor.
- Sensores de temperatura para monitorar a temperatura ambiente e da carcaça do motor.
3 – Aprendizado de máquina que cria modelos de motores durante a operação
- Combinação e interpretação de dados de detecção de alta qualidade para diagnósticos de maior credibilidade.
- Criação automatizada de modelo agnóstico à marca do motor.
- Modelo personalizado que aprende a operação do motor e a sua interação com a carga.
Mais vantagens do sensor inteligente ADI OtoSense
Assim como a solução ADI OtoSense, o sensor inteligente ADI OtoSense também traz outras vantagens quando aplicado em uma indústria. Veja, abaixo, quais são elas.
- Plataforma única para monitorar todos os principais ativos da usina.
- Sinais de amostra a 6,2 kHz a cada 20 minutos, que permitem a identificação de diversas falhas mecânicas e elétricas com alta credibilidade.
- Detecção e identificação de danos, permitindo uma manutenção preditiva eficiente.
- Instalação e configuração rápidas e fáceis, poisnão requer fios ou gateways adicionais e funciona com a maioria dos motores, independentemente da marca.
A solução que apresentamos pode auxiliar na implementação da manutenção preditiva na sua usina de geração de energia ou em outros ambientes industriais. Para saber mais sobre isso, clique aqui e entre em contato com a gente.
Quer conhecer as principais tendências do mercado de geração de energia e ficar por dentro de tudo que está acontecendo nesse setor? Clique aqui e assista ao nosso MacniCast especial sobre esse tema.
Conheça mais sobre a Macnica DHW aqui!